As with ordinary material mechanics calculations, it is possible to calculate whether a structure will break or not, or how much it will deform when a load is applied to it. For example, it is possible to predict whether gravity or load will satisfy the requirement when assembly accuracy is required.
Arms for conveyance, for example, must be designed to minimize the amount of deformation because large displacement of their tips causes less positioning accuracy and difficulty in grasping objects. On the other hand, it is necessary to build them as light as possible considering the operating speed and driving force of the motor. In such cases, lighter and stronger items can be designed by assigning parameters and conducting analysis based on assumed usage conditions.
Heat may also give load. Thermal deformation occurs when the temperature of an object changes, and the amount of deformation is determined by the material’s coefficient of thermal expansion. For example, when you pour boiling water into a glass, the bottom of the glass gets heated and expands, but the top doesn’t, which can cause it to break. Technosolver can analyze such problems as well.
Static load analysis example
Stress analysis during press-in
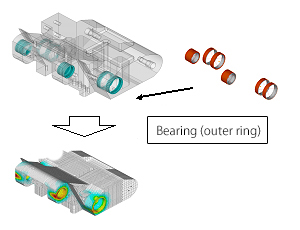
Here shown is stress distribution in a housing of aluminum cast when a bearing is press-fitted into the housing and is a prediction by analysis of possibility of housing cracking.
Stress states can be also determined by calculating when loads are applied to the entire piece or when temperature changes occur, under conditions of stress generated due to fit tolerances.
Static load analysis of composite material structures
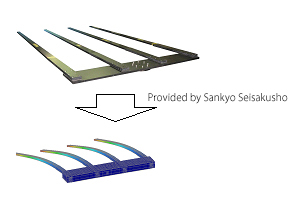
Shown left is an example of static load analysis assuming loads during operation to predict the deformation of a CFRP robot hand for glass transfer used in manufacture of liquid crystal panels.
CFRP components must be evaluated by simulating the direction of the carbon fibers and considering the stiffness and strength that vary with the fiber orientation.
Thermal deformation analysis of electronic boards
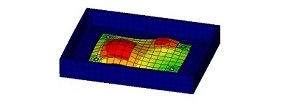
The left figure shows how a board is predicted to deform due to variations in the temperature distributions of the board caused by the heat generated by electronic devices. The temperature distribution obtained from the heat transfer analysis performed separately is used as the input condition.