Strength evaluation integrated tool IOSET
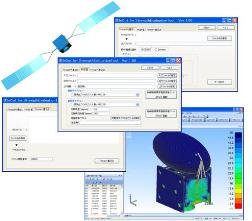
【Static Plate Strength Evaluation Tool】
【Dynamic Plate Strength Evaluation Tool】
【Static Solid Strength Evaluation Tool】
【Dynamic Solid Strength Evaluation Tool】
This software evaluates the strength of plate elements and solid elements based on the analysis results of the general-purpose structural analysis software NASTRAN, and displays the results in the general-purpose pre/post software Femap. Complex strength evaluations of composite materials, such as material failure of carbon fiber reinforced plastic (CFRP) laminates and local buckling of honeycomb plates, can be automatically performed.
Features
Compatible with aerospace industry strength evaluation indicators
Static Plate Strength Evaluation Tool
Perform strength calculations for plate and solid elements and output Margins of Safety (MS).
MS is defined as the Margin of Safety (MS) = [Allowable Stress] / [Applied Stress] – 1.
In order to prevent failure, MS must be positive, and it is widely used as a strength evaluation index in the aerospace industry. For isotropic materials, evaluation is based on Von-Mises equivalent stress, while for composite materials, evaluation is based on Tsai-Wu failure criteria.
Fully Integrated with the General-Purpose Pre-Post Tool Femap
It automatically executes evaluation calculations and displays results through an easy-to-use GUI. By importing calculation results into Femap, it allows for contour displays of strength indicators, summary outputs for properties/materials, and easy identification of strength-critical areas requiring reinforcement.
Streamlining Complex Composite Material Strength Evaluations
For laminated plates containing anisotropic materials such as CFRP panels, stress is calculated for each layer considering fiber orientation, and strength evaluations account for different allowable values in tension and compression directions, determining the worst-case value across all layers. It also simultaneously conducts strength evaluations specific to honeycomb panels. Additional information about the core can be input to determine shear failure of the honeycomb core and the strength against local buckling of the honeycomb panel.
Evaluation Contents
Efficiently perform strength evaluations for isotropic materials, anisotropic materials, laminated plates, and even honeycomb panels (sandwich structures composed of a honeycomb core and thin sheets on both surfaces). Carbon Fiber Reinforced Plastic (CFRP) panels are made by layering sheets containing thinly aligned carbon fibers impregnated with resin. The fiber orientation varies by layer, requiring stress calculations considering fiber direction.
Strength Evaluation Items for Laminated Plates
Material Failure
Strength evaluations are conducted using the strength values entered in material property cards. For isotropic materials, evaluation is based on Von-Mises equivalent stress.
Inter-Laminar Shear Failure
Strength evaluations are performed using the adhesive shear allowable values entered in laminated plate element properties.
Strength Evaluation Items for Honeycomb Panels
There are specific failure modes for honeycomb panels, and each one needs to be evaluated individually. Information about the core, such as cell size, longitudinal elastic modulus in the thickness direction, and shear allowable stress, is input as core information files for these strength evaluations.
Inter-Cell Buckling (Intra-Cell Buckling)
This is a phenomenon where the face sheet of the honeycomb buckles at a cell size level, and it is a failure mode that is more likely to occur with larger cell sizes and thinner face sheets.
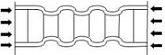
Delamination
This is a phenomenon where the face sheet buckles in conjunction with the core, and it is more likely to occur when using a thick low-density core.
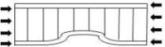
Core Shear
This is a phenomenon where the core undergoes shear failure, and it is a common failure mode that often occurs in areas near fasteners and joints.
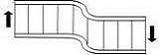
Supported Analysis Items
It supports static load analysis and frequency response analysis output formats. It also supports transient response analysis, which is output in the same format as static load analysis. In frequency response analysis, it is necessary to consider the phase angle of the response to excitation when performing strength evaluations. For example, when the phase is 180 degrees different, the stress reverses in sign, and it is not known which angle is the most critical in terms of strength without calculation. Therefore, for frequency response analysis, you can specify the initial angle and phase increment for calculating angles and evaluate strength at all angles. It is also possible to evaluate by inputting a constant multiple for each analysis frequency. Furthermore, the minimum MS value for all analysis frequencies is consolidated into one analysis set and transferred to Femap, along with the layer number and set number in which it occurred.
Operating Environment
It follows the operating environment of Femap. Compatible Femap versions: Femap V.9.2~V.11.1 Japanese version
OS: Microsoft Windows 8, 8.1, 10, Other: USB port
Components
・Strength Evaluation Integrated Tool [IOSET]
・Static Plate and Solid Element Strength Evaluation Tool [SPSET/SSSET]
・Dynamic Plate and Solid Element Strength Evaluation Tool [DPSET/DSSET]
※The price is for one Node-Locked License. It uses a USB license management device.
We also offer sales for static analysis only or frequency response analysis only. Please feel free to contact us.
For inquiries, please contact us here, or call our company (phone number: 0466-42-6653).